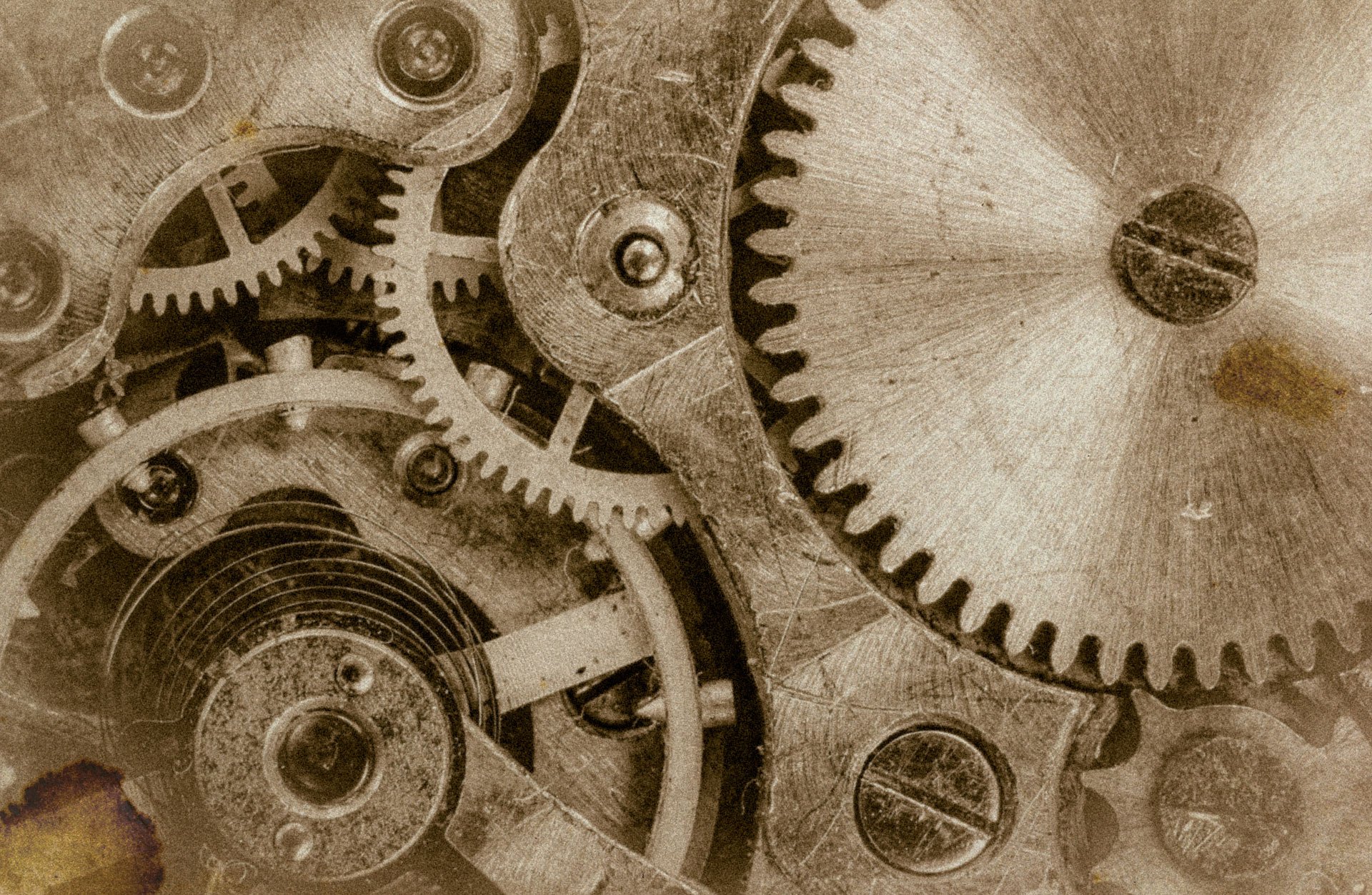
The shortage of maintenance professionals has been under wide discussion for years. Many people working in plant environments have encountered the same challenge: acquiring skilled labour is difficult today. Like all other branches of industry, the maintenance industry is also constantly evolving and progressing. The focus is shifting from reactive maintenance to more predictive and planned scheduled maintenance.
It is clear that the changes taking place in the industry and stricter requirements for uninterrupted production simultaneously also create need for development. Maintenance personnel, both employees and management, are required to possess new skills and competences, as well as have determination and a focus on the development of maintenance.
“Transferring tacit knowledge is a matter of urgency”
[one_half]
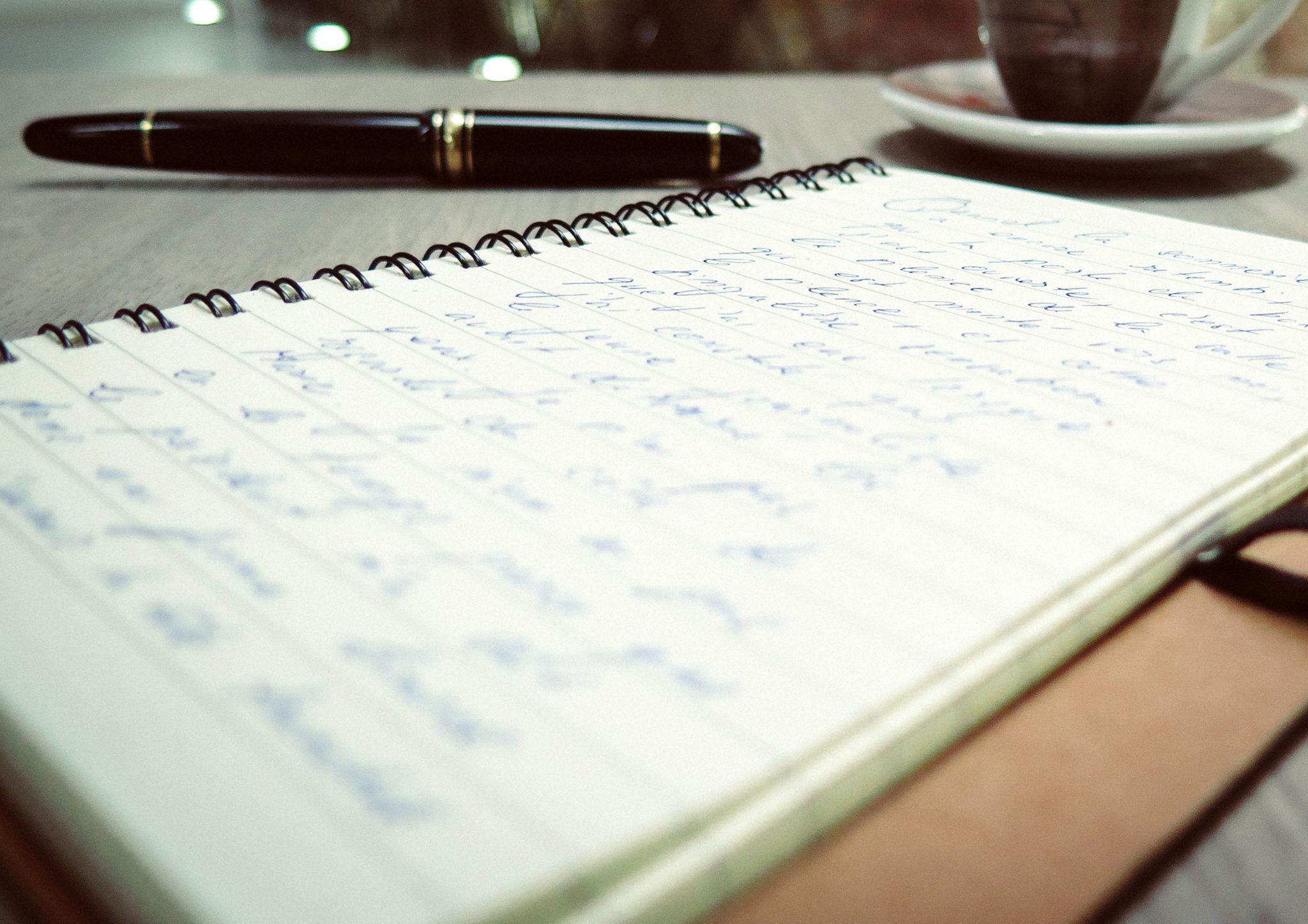
[/one_half]
Particularly at thermal and water plants, working careers are typically long. Employees gather a huge amount of wide-ranged expertise and knowhow of the plant operation and processes. At the same time, the average age of employees is higher than average compared to other branches of industry. The risk of knowledge loss threatens, since there are more and more maintenance professionals approaching retirement in the coming years.
In fact, according to a doctoral dissertation in Tampere University of Technology published earlier this year, transferring tacit knowledge is already a matter of urgency. It is critical to capture knowledge possessed by people reaching retirement to ensure proper functioning of plants. It seems outrageous that knowledge and skills accumulated at best over a 40-year career of a maintenance professional now reaching retirement are at many plants still recorded in a notebook covered by dried coffee stains – if even in it.
Towards digitalisation
Retaining maintenance knowhow and knowledge requires that those who carry the responsibility for the plants must step forward. More prominently than before, they must take responsibility for knowledge management and information sharing. First and foremost, this means learning new ways of operation and change management. Information sharing requires time, efficient tools and – most importantly – right attitudes.
It is a harsh fact that no tool or channel alone can solve the problem of information sharing, if organisations lack a genuine desire, enthusiasm and the right mindset for development. It is understandable that particularly at small plants, the resources available for development are limited. On the other hand, reduced resources force us to question old approaches functioning in this way as an ideal driver for change, which is evitable.
The new generation has tools for better work through digitalisation. Even those accustomed to old patterns can be involved. It is a matter of attitude only.
Sources:
S. Sandelin: “Knowledge Management and Retention: A Case of a Water Utility in Finland.” 2017.